Di cosa sono fatti i forni a legna |
Approfittiamo di questa pagina per dare qualche informazione generale sui materiali utilizzati per la realizzazione di forni, caminetti e barbecue, per lo più ceramica e materiali ceramici, tutti in qualche modo legati a, o derivati da:
L'Argilla
Veramente, più che di argilla bisognerebbe parlare di Argille: tante sono infatti le formazioni sedimentarie descritte da questo termine generico, che nemmeno tra i geologi esiste un accordo definitivo sulla loro classificazione.
Le argille sono infatti, semplicemente, il prodotto del disfacimento delle rocce che costituiscono la crosta terrestre, causato dal vento, dalle piogge o dal gelo, i cui residui formano dei depositi alluvionali la cui composizione può variare notevolmente a seconda della natura delle rocce madri e delle trasformazioni subite nel corso del tempo.
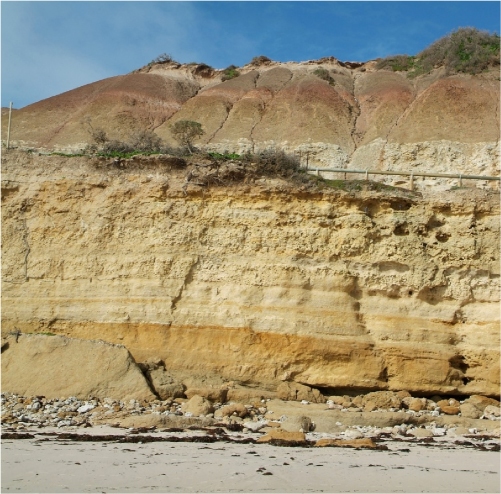
Le argille quindi non sono rare: insieme al fango ed al terriccio sono il costituente principale del suolo terrestre. Caratteristica fondamentale per la classificazione come argille è l'estrema finezza delle particelle costituenti la massa, che non devono superare, in media, i 0,002 mm di diametro (molto più piccole delle particelle costituenti il fango). Le particelle sono così sottili, che se un po' di argilla viene disciolta in acqua, può impiegare giorni e giorni a depositarsi, e qualche particella resterà comunque in sospensione nel liquido. Questa estrema finezza è responsabile di alcune delle proprietà meccaniche delle argille: si può dire che praticamente qualunque roccia, ridotta in polvere così impalpabile, assumerebbe in parte le caratteristiche per cui le argille sono conosciute: la capacità di assorbire acqua in grandi quantità, la plasticità (cioè la capacità, quando imbevuta di acqua, di formare una massa atta ad essere modellata conservando la forma impressale), l'indurimento e la diminuzione di volume in seguito ad essiccazione e cottura, l'impermeabilità a secco.
Le argille vere e proprie, tuttavia, derivano dal disfacimento dei feldspati, gruppo di minerali cristallini estremamente comune (da solo costituisce circa il 60% delle rocce della crosta terrestre), le cui caratteristiche chimiche forniscono alle argille le loro più specifiche proprietà. I feldspati sono costituiti da alluminosilicati di potassio, sodio e calcio, più piccole percentuali di altri elementi.
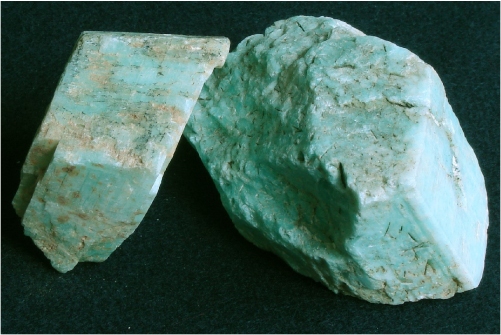
Le argille contengono quindi sopratutto ossidi idrati di silicio e alluminio, con l'aggiunta di altri composti che contribuiscono a determinarne le caratteristiche, a seconda della loro presenza e relativa concentrazione, come carbonato e solfato di calcio, pirite, ossidi di ferro, sodio, manganese, titanio e potassio, oltre a sostanze organiche derivate da detriti vegetali o da infiltrazioni di humus.
Quasi tutte le argille contengono inoltre anche minime percentuali di oligoelementi come argento, oro, ferro, mercurio, piombo, rame e stagno.
I componenti secondari delle argille sono responsabili della colorazione (esistono argille bianche, grigie, verdi, brune e brunorossastre, rosse e blu), oltre ad influire variamente sulle caratteristiche principali (plasticità, temperatura di fusione, etc).
I componenti fondamentali delle argille, gli idrosilicati di alluminio, hanno una struttura cristallina stratificata che conferisce alle particelle un aspetto piatto e sottile. La struttura cristallina, grazie anche alle sue particolari capacità elettriche ( abbondanza di legami non saturi), è in grado di assorbire grandi quantità di molecole estranee, specialmente acqua, mentre la 'piattezza' incrementa la plasticità delle argille: le superfici piatte aiutano le particelle ad aderire tra loro, come due fogli di giornale bagnati.
Quando le argille vengono sottoposte a riscaldamento, ha inizio la disidratazione, seguita, con l'aumentare della temperatura, da un serie di variazioni strutturali, che si completano, a temperatura sufficientemente elevata, con la formazione di nuove fasi minerali e con una profonda modificazione chimica.
La cottura provoca una diminuzione di volume e di peso, ed un aumento di densità, solidità e impermeabilità. Si osserva anche un cambiamento nel colore, che vira verso il bianco, il crema, il marrone chiaro, il rosso, fino al quasi nero (in alcuni tipi di mattoni). Le variazioni chimiche dipendono, oltre che dalla specifica composizione dell'argilla, dalla temperatura raggiunta e dal tempo di cottura. In generale si ottiene una ricristallizzazione, con la creazione di una massa di fondo vetrosa disseminata di cristalli di silice e di mullite (un ossido di silicio e alluminio), le cui caratteristiche fisiche e meccaniche sono profondamente diverse da quelle dell'argilla cruda.
Tanto per capire cosa si intende per ricristallizazione, si tenga presente che alcuni composti chimici hanno la proprietà di avere gli atomi componenti la struttura disposti in un reticolo regolare invece che distribuiti casualmente nello spazio. I reticoli cristallini possono variare per forma e disposizione, e, generalmente, ad ogni diversa disposizione corrispondono diverse proprietà fisiche e meccaniche. Ad esempio, la grafite è una forma cristallina del carbonio puro, utilizzata, fra l'altro, per le mine delle matite. Una forma cristallina diversa del carbonio puro dà origine ai diamanti.
Per restare nell'ambito dei materiali componenti le argille, l'ossido di alluminio, Al2O3, conosciuto come allumina, è una polvere biancastra impalpabile componente fondamentale di tutti i materiali refrattari comuni.
La forma cristallina dell'ossido di alluminio, il corindone, è una pietra dura, che nelle sue varietà più pregiate, il rubino (che deve il suo colore rosso a tracce di cromo) e lo zaffiro (la cui colorazione blu è dovuta a tracce di ferro e titanio) è la pietra colorata più preziosa esistente sul mercato, caratterizzata da una durezza e da una resistenza paragonabili a quelle del diamante.
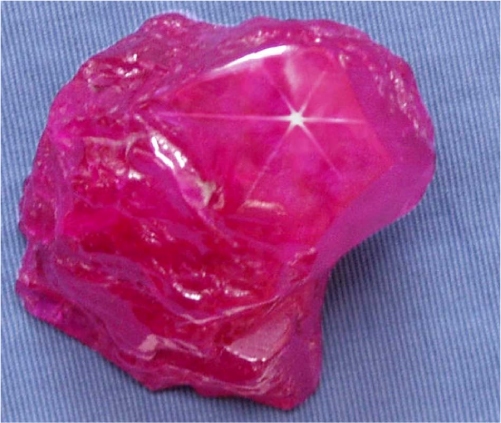
L'impiego delle argille
Il campo di impiego delle argille è vastissimo, dalla medicina naturale (alcuni tipi di argilla hanno capacità antisettiche, battericide e cicatrizzanti) alla cosmesi ed alle cure termali (per i bagni di fango vengono utilizzati impasti di varie argille), dalla produzione artistica (la creta degli scultori non è altro che argilla), alla lavorazione della carta (dove alcuni componenti delle argille sono utilizzati come sbiancanti e patinanti) all'industria delle costruzioni ed alla produzione di materiali ceramici e refrattari, che è quello che ci interessa di più.
I materiali ceramici
La classificazione dei materiali ceramici è complessa quasi quanto quella delle argille. Tanto per curiosità, diamole una rapida scorsa.
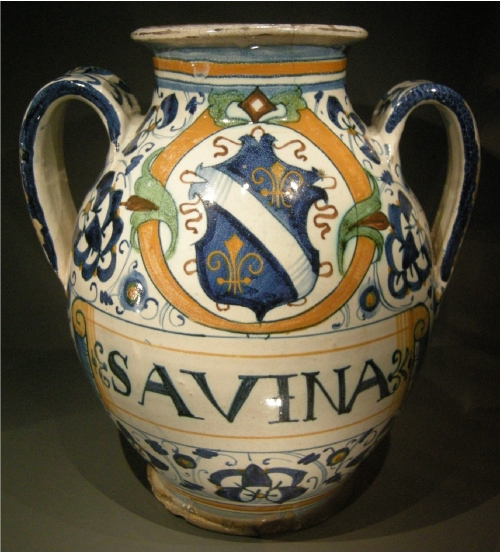
Sono chiamati oggi prodotti ceramici tutti quelli ottenuti da materiali inorganici non metallici, generalmente mediante riscaldamento ad alta temperatura. Con tale ampia definizione si intendono perciò sia quelli tradizionali, ottenuti per cottura di argille più o meno pure o purificate con aggiunta o meno di altre sostanze, sia quelli di più recente utilizzazione, ottenuti con processi di sintesi (sinterizzazione), diversi sia dal punto di vista chimico che strutturale, e che esulano dal nostro campo di interesse.
La classificazione dei prodotti ceramici tradizionali li divide in prodotti a pasta porosa od a pasta vetrificata dopo la cottura. La pasta porosa si presenta opaca e terrosa alla frattura, permeabile ai gas ed ai liquidi, facilmente assorbente.
La pasta vetrificata si presenta compatta e lucente alla frattura, impermeabile ai fluidi, non assorbente e richiede una temperatura di cottura decisamente più alta.
Se la pasta porosa è bianca, abbiamo le terraglie, solitamente verniciate (vasellame vario); se la pasta porosa è colorata e verniciata , abbiamo le faenze che, se rivestite da uno smalto opaco, sono conosciute come maioliche, alle quali appartengono molti prodotti ceramici d'arte (maioliche di Faenza, di Gubbio, di Delft, etc). Se la pasta porosa è colorata, ma non verniciata, abbiamo le terrecotte (mattoni e laterizi) ed i refrattari.
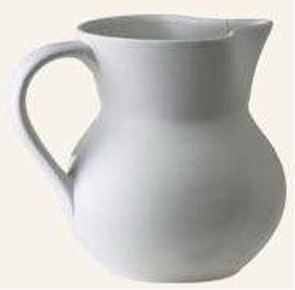
Se la pasta vetrificata è bianca, abbiamo la porcellana, anzi, le porcellane, perchè tantissime sono le varianti, verniciate o meno. Per la verità la componente fondamentale della porcellana è il caolino, una roccia costituita sopratutto da caolinite, un idrosilicato di alluminio molto puro e bianchissimo, che deriva il suo nome dalla località cinese di Kauling, dove per la prima volta fu estratta, e che costituisce il principale componente delle porcellane cinesi.
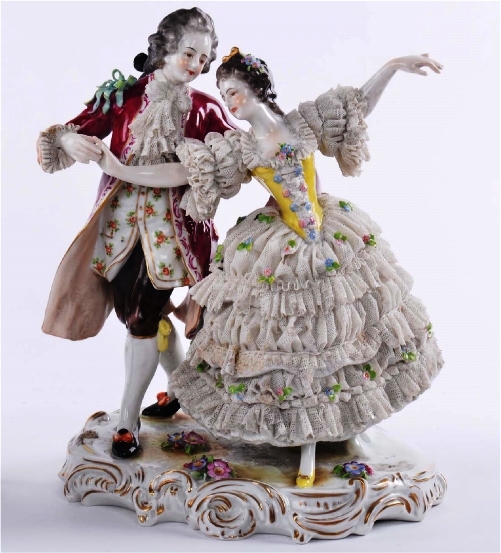
In realtà molte argille contengono caoilinite, ma sempre accompagnate da impurità, sopratutto ossidi di ferro, presenti in forma talmente suddivisa da renderne l'eliminazione impossibile, e l'utilizzo dell'argilla per realizzare porcellane altrettanto impossibile. Le argille caoliniche sono comunque particolarmente pregiate, utilizzate per la realizzazione di refrattari e di grès artificiali. Se il contenuto di ferro è abbastanza basso, sono utilizzate nella produzione di terraglie.
Infine, se la pasta vetrificata è colorata, abbiamo il grès, che può essere grès naturale, se ottenuto da una unica argilla, od artificiale, se ottenuto da cottura di miscele appropriate. I grès sono molto resistenti agli agenti aggressivi e trovano impiego nell'industria chimica e nelle fognature. Nell'edilizia sono usati per le pavimentazioni.
Ricapitolando:
Prodotti Ceramici tradizionali |
Prodotti a tessitura porosa |
Non rivestiti | Non strutturali (terrecotte) |
Strutturali (laterizi, refrattari) | |||
Terraglie speciali (filtri, vasi porosi) | |||
Rivestiti | Faenze | ||
Maioliche | |||
Terraglie | |||
Prodotti a tessitura compatta |
Non rivestiti | Grès per pavimentazioni | |
Porcellane per usi tecnici | |||
Rivestiti | Grès per fognature | ||
Grès di qualità (vasellame domestico) | |||
Porcellana |
La lavorazione e la produzione di laterizi e refrattari
Nella preparazione di una pasta per prodotti ceramici i materiali comunemente impiegati sono tre: un legante, un inerte, un fondente, cioè molto spesso, caolino, quarzo e feldspato. Ciascuno di questi tre elementi possiede qualità particolari. L'argilla e/o il caolino (cioè in realtà gli idrosilicati di alluminio, leganti e plastificanti) per aggiunta di acqua conferisce alla pasta la plasticità, cioè la modellabilità, e tiene insieme l'impasto.
Il quarzo (od altri inerti, come sabbia silicea, cocciopesto, polveri di argilla già cotta, etc), ha la proprietà di diminuire il ritiro della pasta durante la cottura (l'argilla pura, di per sé, tende a diminuire notevolmente di volume durante l'essiccamento e la cottura), il feldspato (o altri fondenti, come il calcare, l'ossido di ferro, i fosfati), ha la proprietà di abbassare la temperatura di cottura dell'impasto.
Nelle argille naturali di migliore qualità questi tre componenti sono già presenti, in molti altri casi si interviene correggendo la composizione originale, o addirittura creando un impasto ad hoc partendo da componenti separati, come avviene per la produzione di molti refrattari e di alcune porcellane. Per la verità, così tante sono le argille disponibili e così tante le modificazioni a cui possono essere sottoposte, variando in modo quasi infinito la qualità e le proporzioni degli elementi componenti, che più che di chimica si dovrebbe forse parlare di alchimia. Non c'è praticamente produttore di ceramiche che non abbia le sue proprie formule, frutto spesso dell'esperienza, della tradizione e di una lunga serie di tentativi ed errori che non di un rigoroso procedimento scientifico, e altrettanto spesso gelosamente custodite
Le argille da utilizzare non devono contenere sostanze organiche in granuli di notevoli dimensioni perché esse, durante la cottura, bruciano lasciando vuoti che rendono i mattoni porosi e poco resistenti. Il tenore di carbonato di calcio non deve superare il 14-15% perché durante le cottura può liberare CO2, formando CaO che si idrata lentamente aumentando di volume, anche dopo molto tempo dopo la messa in opera, con conseguente sgretolamento del manufatto.
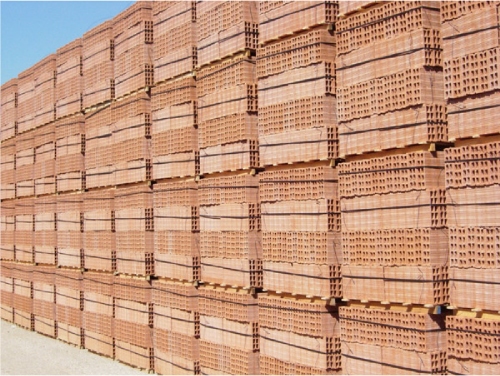
Un tempo l'argilla estratta veniva lasciata alle intemperie (maturazione o ibernazione) in modo che l'alternanza gelo, disgelo, pioggia e sole, ne modificasse lo stato colloidale aumentandone l'elasticità. Attualmente la maturazione si integra o si sostituisce con trattamenti meccanici che consistono nella disgregazione della massa. Si interviene anche correggendo l'argilla, normalmente troppo plastica (grassa), aggiungendo smagranti come sabbia o silice.
Un tempo l'argilla estratta veniva lasciata alle intemperie (maturazione o ibernazione) in modo che l'alternanza gelo, disgelo, pioggia e sole, ne modificasse lo stato colloidale aumentandone l'elasticità. Attualmente la maturazione si integra o si sostituisce con trattamenti meccanici che consistono nella disgregazione della massa. Si interviene anche correggendo l'argilla, normalmente troppo plastica (grassa), aggiungendo smagranti come sabbia o silice.
Durante la fase di formatura la pasta viene immessa ancora umida in macchine del tipo a trafila. dove viene pressata e fatta uscire da un orifizio avente la sezione del pezzo che si vuole produrre. Si ottiene così un nastro continuo che viene quindi tagliato in pezzi della lunghezza voluta. I pezzi ottenuti vengono fatti essiccare lentamente per evitarne la deformazione. Attualmente l'essiccazione si ottiene artificialmente, disponendo il materiale in opportune camere ad aria calda. Quindi si passa alla fase di cottura, che si effettua a temperature crescenti sino ad un massimo di circa 1000°C, per un tempo medio di 8 ore. La cottura lenta e graduale serve ad evitare la frattura dei pezzi, possibile con un riscaldamento troppo rapido. I forni attualmente utilizzati sono a tunnel: il materiale da cuocere, caricato su carrelli, percorre il forno in senso contrario al flusso dei gas caldi liberati dal focolaio, ed è perciò sottoposto a temperature crescenti e quindi ad una cottura graduale ed uniforme. Oltrepassato il focolaio il materiale cotto incontra aria fredda aspirata dall'esterno, e viene gradualmente raffreddato.
I materiali refrattari
Col termine 'refrattari' si intendono quei materiali in grado di resistere a temperature particolarmente elevate (nell'ordine di almeno 1000°C) senza subire fratture o deformazioni. Da questo punto di vista, si può dire che praticamente qualunque prodotto ceramico possiede almeno un certo grado di refrattarietà, se non altro per essere stato prodotto con una cottura a temperatura elevata.
Tuttavia non c'è dubbio che i materiali necessari alla realizzazione di forni, barbecue o camini siano sottoposti a sollecitazioni termiche e meccaniche decisamente più elevate di quelle cui sono sottoposti i comuni laterizi impiegati nell'edilizia (per non parlare dei materiali necessari per la realizzazione di altoforni per la siderurgia, od impiegati nelle industrie chimiche o aerospaziali) e richiedono dunque tecniche di lavorazione e produzione specifiche, con particolare attenzione alla composizione dell'impasto ed alla fase di cottura
Le caratteristiche fondamentali di un materiale refrattario devono essere: l'invariabilità di volume, e quindi un basso coefficiente di dilatazione a temperatura, per assicurare la stabilità dei manufatti realizzati; una buona resistenza alle sollecitazioni meccaniche, specie alle alte temperature (condizione nella quale, invece, molti comuni laterizi diventano più fragili); una porosità minima, per resistere alle azioni chimiche e corrosive delle sostanze con cui vengano a contatto (prodotti della combustione, condense acide, etc).
Un materiale refrattario di qualità viene dunque ottenuto controllando la natura chimica dei componenti, eliminando le impurità presenti nella maggior parte delle argille, sottoponendo il materiale ad una lavorazione meccanica e ad una cottura attentamente controllate.
La composizione chimica dei refrattari può variare considerevolmente, a seconda dello specifico campo di utilizzo, ma generalmente la percentuale di allumina (ossido di alluminio Al2O3) e di silice (ossido di silicio SiO2) è alta, essendo questi i componenti fondamentali in grado di conferire refrattarietà, mentre la percentuale di impurità organiche e di altri ossidi (ossidi di calcio, potassio, sodio, magnesio, ferro, etc, tutti comunemente presenti nelle argille) è mantenuta bassa. Le impurità e gli ossidi possono essere sottoposti a modificazioni chimiche alle alte temperature, o reagire chimicamente con i prodotti della combustione, causando un rapido deterioramento del refrattario. Nei comuni laterizi, impiegati in condizioni di temperatura ambiente, una assai maggiore percentuale di impurità o di ossidi estranei può essere tollerata.
Anche la lavorazione meccanica influisce sulla resistenza del refrattario. Una grana fine ed omogenea ed una compressione notevole durante la formatura conferiscono resistenza alla compressione e durabilità nel tempo.
Infine, la realizzazione dell'impasto ed il processo di cottura sono particolarmente importanti. I comuni laterizi sono cotti a temperature che difficilmente completano in processo di vetrificazione degli idrosilicati alluminio. Ne consegue che l'esposizione a forti temperature può avviare un processo di ulteriore vetrificazione incontrollata, con modifiche nel volume del pezzo, ulteriori ritiri dell'impasto legante, o rigonfiamenti dovuti a reazioni chimiche in presenza di eventuali impurità, che compromettono le qualità meccaniche del pezzo e la stabilità dell'intera struttura. Per ovviare a questo problema, l'impasto del materiale refrattario da sottoporre a formatura viene realizzato a secco, mescolando piccole quantità di paste leganti con la cosiddetta chamotte, che non è altro che un materiale refrattario già sottoposto a cottura sino al punto da non poter più subire ulteriori contrazioni di volume, e quindi sbriciolato ed utilizzato come inerte. L'impasto viene poi leggermente umidificato e sottoposto a formatura a forte compressione e successiva ulteriore cottura.
A seconda della qualità di chamotte e di pasta legante utilizzate, della forza di compressione impiegata, della grana dell'impasto prescelta e della temperatura di cottura finale utilizzata, si otterrano prodotti refrattari di caratteristiche anche molto diverse. Vi sono quindi in commercio una notevole varietà di prodotti, la cui classificazione non è sempre facilissima. L'utilizzabilità di un refrattario per uno specifico uso dipende dalle sue caratteristiche meccaniche e dal suo grado di refrattarietà.
In linea generale, ad esempio, un refrattario utilizzato per il rivestimento di forni dove si raggiungono alte temperature per lunghi periodi, o dove vi può essere contatto con metalli fusi, dovrebbe avere una grana finissima, alta densità e consistenza plastica; dove invece la caratteristica principale debba essere la resistenza a violenti sbalzi di temperatura, una grana più grossolana ed un plasticità inferiore è raccomandabile. Mattoni refrattari la cui specifica caratteristica debba essere la capacità isolante, in condizioni in cui la temperatura sia variabile, ma mai estremamente alta, vengono realizzati mescolando l'impasto argilloso con segatura di legno, che bruciando durante la cottura, restituisce una tessitura estremamente porosa e dotata di bassissima conducibilità termica.
Materiali refrattari diversi trovano diverso uso nella realizzazione rispettivamente di stufe, camini e forni, e, come quasi sempre accade in un campo in cui la tradizione e l'esperienza personale dei costruttori e dei produttori contano molto, esistono scuole di pensiero assai diverse circa il prodotto più adatto ad un determinato scopo.
I mattoni ad alto contenuto di allumina sono particolarmente resistenti al calore e all'abrasione, sono utili nelle stufe ma possono avere controindicazioni se utilizzati nella realizzazione di piani base di forni dedicati alla cottura del pane: l'alto contenuto di allumina rende il mattone estremamente conduttivo, il che trasferisce una eccessiva quantità di calore al fondo delle pagnotte, che può bruciare prima che il corpo della pagnotta sia cotto. Inoltre, i refrattari ad altissimo contenuto di allumina sono meno resistenti nel tempo ai cicli di raffreddamento e riscaldamento. In generale, il contenuto di allumina nei materiali refrattari per la realizzazione delle basi dei forni non dovrebbe superare il 30%. Alcuni produttori di forni preferiscono realizzare materiali che sono perfino meno resistenti dei mattoni comuni alla temperatura, ma maggiormente resistenti agli shock termici. In sostanza, anche un comune mattone di buona qualità viene talvolta utilizzato per la realizzazione di almeno alcune parti di un forno.
I mattoni refrattari
Il più comune materiale refrattario in commercio è il mattone refrattario, che viene prodotto non solo in una quantità di forme e dimensioni diverse (mattoni, listelli, cunei, tavelle, etc, anche antichizzati) ma anche con una notevole variabilità nella composizione e nella cottura.
Con l'aiuto dell 'Alfarefrattari, che è uno dei maggiori fabbricanti nazionali di refrattari, daremo un'occhiata ai prodotti più comuni
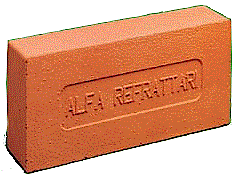
Mattoni di qualità rossa, utilizzati per il rivestimento di focolari di caminetti e barbecue, per la realizzazione di muretti e spallette a vista di caminetti, per i davanzali ed i piani fuoco dei forni a legna.
Resistenza termica 1050 °C, resistenza alla
compressione 540 kg/cmq, peso circa 2 Kg/dmc, conducibilità termica
λ 1,63
Il
colore rosso, che è voluto, è dovuto alla presenza di piccole
quantità di ossidi di ferro.
Mattoni di qualità bianca, utilizzati per focolari di caminetti e barbecue, per le pareti di forni a legna, per muretti e spallette di caminetti, forni e barbecue.
Resistenza termica 1300 °C, resistenza alla compressione 580 kg/cmq, peso circa 2 kg/dmc, conduttività termica λ 1,70.
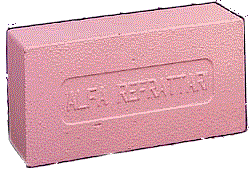
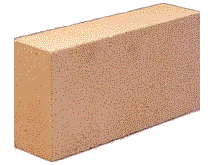
Mattone silico-alluminoso, ad alto contenuto di allumina, utilizzato principalmente in fumisteria, per la realizzazione di caldaie e condotte fumi, o per l'industria edilizia, nel rivestimento di forni industriali.
Resistenza termica 1600 °C, peso circa kg 2,2/dmc
Mattone isolante, disponibile sia in colore rosso che bianco, utilizzato per isolare termicamente e dove non si sia in presenza di fuoco diretto o grandi sforzi meccanici.
Peso tra 0,4 ed 1 Kg/dmc
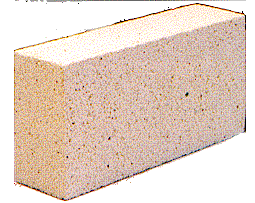
Cementi e malte
Per cemento in senso lato si intende qualunque sostanza in grado di aderire a frammenti o parti di materiali non di per sè adesivi, e di unirli in una massa coerente. Il termine si può applicare a qualunque miscela adesiva utilizzata per unire oggetti o parti di oggetti, per esempio i cementi odontoiatrici, ma, quando usato in ingegneria, o senza specificazioni, indica sempre il cemento idraulico, ovvero un cemento in grado di resistere all'azione dell'acqua ed impiegato nell'edilizia.
Era cosa conosciuta ai costruttori dei tempi più antichi che alcuni tipi di calce, quando rappresi, erano in grado di resistere all'azione dell'acqua, cioè avevano proprietà idrauliche. Era anche risaputo che tali proprietà idrauliche potevano essere conferite alla calce comune miscelandola con materiali silicei come pozzolana o tufo. Abbiamo qui le due classi in cui i cementi idraulici possono essere divisi, il cemento pozzolanico ed il cemento Portland.
Cemento Pozzolanico
Quando il gesso puro od il calcare vengono riscaldati ad una temperatura di circa 1000°C, in modo da eliminare tutto l'acido carbonico in essi contenuto, si ottiene ossido di calcio, la cosiddetta calce viva, un materiale estremamente reattivo ed ustionante, che in certe applicazioni viene usata come tale, ma in genere viene trattata con acqua, con la quale reagisce violentemente, generando idrossido di calcio, la cosiddetta calce estinta o spenta ( oppure, alla romana, 'smorzata', da cui il termine 'smorzo', conferito a Roma ai rivenditori di materiale edile che fornivano questo prodotto). Il processo di estinzione può essere effettuato usando soltanto la quantità di acqua strettamente necessaria all'idratazione, in modo da ottenere la calce idrata in polvere; ovvero utilizzando un eccesso di acqua, ottenendo così una pasta morbida, detta grassello. Mescolando la calce idrata con sabbia ed acqua si ottiene una semplice malta, in cui la sabbia ha solo funzione di inerte, per evitare un eccesso di ritiro durante l'essiccamento. L'azione cementante è dovuta semplicemente all'essiccamento della calce, non intervenendo alcuna particolare reazione chimica. L'indurimento è dovuto all'assorbimento di acido carbonico dall'aria da parte della calce, con formazione di carbonato di calcio, un fenomeno comunque abbastanza superficiale. La malta ottenuta con pura calce non è in grado di resistere all'azione dell'acqua, e quindi ha un impiego limitato. Tuttavia, se la calce, in presenza di acqua, viene miscelata con silice in forma attiva, formerà dei silicati di calcio anidri in grado di resistere all'azione dell'acqua. La miscela di calcio e silice attiva è il cemento pozzolanico, che può essere ottenuto mescolando calce con prodotti naturali quali pomice, tufo e, appunto, pozzolana, che contengono tutti alte percentuali di silicati idrati.
Cemento Portland
Il nome fu imposto a questa classe di cementi dal muratore inglese Joseph Aspdin, che nel 1824 brevettò un composto di calcari ed argille calcinati, cui diede il nome di Cemento Portland semplicemente perchè il colore del composto ricordava quello di una pietra naturale da costruzione così chiamata.
Il cemento Portland, che è il più comune e pregiato cemento per edilizia in uso, differisce in parte dal cemento pozzolanico. E' prodotto riscaldando al alte temperature (circa 1500 °C) una miscela intima di materiali calcarei ed argillosi, che possono essere di varia provenienza (gesso, calcare, marne, argilloscisti, etc), purché la corretta proporzione tra calcio, silice ed allumina sia mantenuta. La proporzione corretta tra i componenti oscilla entro questi limiti: ossido di silicio 20-24%, ossido di alluminio + ossido di ferro 7-11%, ossido di calcio 63-67%. Il prodotto così ottenuto (clinker) viene quindi macinato sino ad ottenere una polvere finissima, cui viene aggiunta una certa percentuale di gesso al solo scopo di regolare il tempo di presa del cemento. La cottura produce silicati ed alluminati di calcio, che hanno la proprietà di reagire chimicamente con l'acqua formando una massa dura simile alla pietra. Varie sono le reazioni chimiche che avvengono nell'impasto, che richiedono anche un certo tempo per completarsi. In generale si calcola che dopo 28 giorni dal getto circa l'80% dell'impasto abbia reagito chimicamente ed abbia fatto 'presa'.
Le proprietà meccaniche dell'impasto indurito rappresentano le caratteristiche più importanti. Esse risultano, come anche quelle di presa, influenzate da vari fattori, quali la costituzione mineralogica del cemento e la finezza della macinazione. In breve si può dire che la resistenza meccanica degli impasti aumenta con la finezza di macinazione del cemento usato, con la diminuzione, entro certi limiti, della quantità d'acqua impiegata e, sempre entro certi limiti, con la stagionatura dell'impasto. Anche i vari tipi di alluminati e silicati di calcio presenti nell'impasto, e le loro relative proporzioni, influenzano le specifiche proprietà meccaniche di un cemento portland, che avrà diversa composizione e trattamento a seconda dell'impiego previsto.
Mescolando il cemento portland con sabbia, ghiaia, pietrisco od altri inerti, si ottengono malte e calcestruzzi di diverse caratteristiche che trovano il più vario impiego in edilizia.
Le malte
Assai raramente, per non dire mai, i cementi vengono utilizzati puri. Piccole quantità di cemento puro vengono utilizzate per stuccature o piccole riparazioni. Tuttavia l'utilizzo del cemento puro non è consigliabile per motivi pratici, tecnici ed economici.
I cementi hanno una alta percentuale di ritiro durante l'essiccazione, il che può compromettere la qualità del risultato finale, specie in getti di grandi dimensioni. Inoltre il cemento è decisamente più costoso rispetto ad altri materiali utilizzabili per la costruzione, come sabbia, ghiaia e pietrisco. Infine il mescolamento con altri materiale conferisce al cemento proprietà diverse, sfruttabili in differenti situazioni.
Sfruttando l'alto potere legante del cemento, piccole quantità dello stesso possono essere miscelate a grandi quantità di inerti senza compromettere la resistenza meccanica finale del prodotto. La presenza dell'inerte riduce il ritiro della massa durante l'essiccazione a livelli trascurabili, diminuisce il costo di costruzione, fornisce all'impasto diverse caratteristiche a seconda dei materiali impiegati. La miscela del cemento con inerti di vario genere viene detta malta o calcestruzzo. L'uso di inerti dalle particolari proprietà, come argilla espansa, vermiculite o perlite, di seguito descritte, fornisce agli impasti così ottenuti particolari capacità di leggerezza, resistenza od isolamento termico, etc.
Malte e cementi refrattari
Molti muratori non hanno familiarità con la malta refrattaria. Forni e caminetti vengono spesso costruiti utilizzando il cemento Portland, magari aggiungendo piccole quantità di argilla o di terra refrattaria per rendere il cemento 'refrattario'.
Il problema del cemento Portland è che non è in grado di resistere ai forti sbalzi termici. Stranamente, il cemento Portland mantiene le sue elevate caratteristiche meccaniche sino a temperature molto elevate, ma è durante il successivo raffreddamento che avviene il deterioramento. Dopo svariati cicli di riscaldamento e raffreddamento tutto quello che rimane della malta realizzata col cemento Portland è la sabbia, senza più nulla o quasi del cemento legante originale. La malta non ha più la forza di tenere assieme i mattoni, che finiscono per muoversi od uscire dalla loro sede, specie se tra l'uno e l'altro era stato inserito uno strato abbondante di malta. A questo punto si tende a sostituire l'intero rivestimento del focolare o del forno, mentre tutto quello che bisognerebbe fare è utilizzare la giusta malta refrattaria.
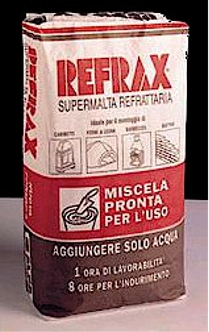
Le malte refrattarie, infatti, utilizzano leganti che non si deteriorano col calore, ma che anzi tendono ad aumentare la propria capacità di presa quando sottoposti ad alte temperature. Per di più, l'uso di malte refrattarie rende la costruzione più semplice e rapida, e quindi più economica.
Le malte refrattarie, ad esempio, 'tirano' molto più rapidamente del cemento Portland. In particolare, le malte a base di silicato di sodio non sono malte idrauliche, cioè non tirano a seguito di una reazione chimica in presenza di acqua come le malte ordinarie, ma si essiccano per azione dell'aria. Questo consente di utilizzare strati di malta anche di pochi millimetri e di non bagnare preventivamente i mattoni, senza che questo comprometta in alcun modo la capacità di presa, che è talmente rapida che pochi secondi dopo aver posizionato un mattone ci vuole già un certo sforzo per rimuoverlo.
Anche le malte refrattarie idrauliche, comunque, hanno tempi di presa molto rapidi. La malta pronta Refrax dell'Alfacaminetti, ad esempio, raggiunge una presa del 70% dopo poco più di un ora, laddove il cemento Portland richiede quasi un mese di tempo per raggiungere la stessa percentuale di presa.
In commercio si trovano sia cementi puri che malte refrattarie pronte. Per un uso 'amatoriale' è raccomandabile l'impiego di una malta pronta, seguendo scrupolosamente le istruzioni del produttore. La composizione è simile all'impasto utilizzato per realizzare mattoni, un cemento legante unito ad una percentuale di chamotte ( in genere 40% e 60%). Al termine del lavoro, l'eventuale eccesso di malta può essere facilmente ripulito con una spugna imbevuta d'acqua.
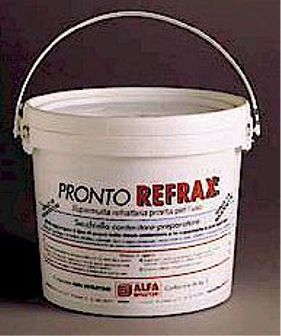
Il cemento alluminoso
Una menzione particolare merita il cemento alluminoso, o cemento 'fuso', così chiamato per la particolare tecnica di produzione. Al contrario del cemento Portland, che viene prodotto a partire da una miscela di calcari ed argille calcinati, il cemento alluminoso viene ricavato da una miscela di calcari e bauxite, quindi con una alta percentuale di allumina, riscaldata ad altissime temperature sino a raggiungere lo stato liquido (fuso), colata in lingotti, raffreddata e macinata per essere ridotta in polvere pronta per l'uso. I componenti chimici del cemento alluminoso sono gli stessi del cemento Portland, da cui però si differenzia per l'alta percentuale di alluminio (dal 40 all'80 %) e per i particolari legami chimici che il calcio contenuto nel calcare e l'alluminio presente nella bauxite formano in seguito alla fusione, producendo alluminati di calcio in una forma e varietà non riscontrabili nel comune cemento Portland.
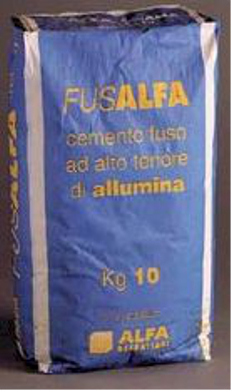
Il risultato è un cemento idraulico dalle caratteristiche eccezionali: la presa è rapidissima, dopo 24 ore la durezza del cemento alluminoso è superiore a quella del cemento Portland dopo 28 giorni; la resistenza agli agenti corrosivi acidi ed all'acqua è molto più alta; sviluppando moltissimo calore durante la presa, può essere utilizzato anche a diversi gradi sottozero, al contrario del Portland, che teme le gelate durante i getti; la resistenza meccanica ed alla abrasione sono superiori; possiede una altissima refrattarietà.
Si direbbe il cemento ideale, e ci si potrebbe domandare perchè mai non abbia soppiantato completamente il cemento Portland nella maggior parte delle applicazioni, se non fosse per un problema, che rende il cemento alluminoso inutilizzabile in molte applicazioni strutturali: buona parte degli alluminati di calcio idrati formatisi molto rapidamente durante la reazione del cemento con l'acqua non sono stabili a temperature superiori ai 20°C.
In queste condizioni, questi alluminati si modificano chimicamente, rilasciando acqua e producendo dei vuoti nella struttura altrimenti estremamente densa del cemento. La porosità e la permeabilità all'acqua aumentano di molto e rapidamente, riducendo proporzionalmente durabilità e resistenza meccanica del cemento.
Può sembrare strano che un cemento dalle altissime capacità refrattarie possa perdere così drammaticamente le proprie capacità meccaniche a temperature tutto sommato così basse. Tuttavia, refrattarietà e resistenza meccanica sono caratteristiche diverse. Temperature superiori ai 20°C fanno perdere al cemento alluminoso parte dell'acqua che forma i legami chimici degli idrati di calcio e alluminio, tuttavia il cemento non si disgrega completamente, come accadrebbe al Portland, e può mantenere la capacità protettiva alle alte temperature. Può dunque essere impiegato laddove non occorra una resistenza meccanica particolare, come additivo nelle malte tradizionali, per realizzare intonaci refrattari, per lavorare in climi freddi, realizzare pavimentazioni altamente resistenti alla abrasione, etc.
Una ultima particolarità: se sottoposto a temperature superiori ai 1000°C, le sue caratteristiche mutano completamente ancora una volta. A questa temperatura la massa del cemento sinterizza, creando legami di tipo ceramico, come nei mattoni refrattari. La resistenza meccanica sia alla compressione che alla tensione cresce di nuovo, sino a raggiungere ed addirittura superare quella originale. Se raffreddato lentamente, mantiene le nuove proprietà acquisite.
Insomma, un prodotto particolare che, se utilizzato da mani esperte, trova impieghi per i quali può essere altamente raccomandato.
Gli inerti
Argilla espansa
L'argilla espansa è un aggregato naturale che si ottiene dalla cottura in forno di particolari argille, denominate 'vari colori', che hanno la particolarità di adsorbire acqua ed altri materiali che rilasciano gas nella fase di cottura. L'argilla cruda viene immessa in un forno rotante dove viene riscaldata a temperature di circa 1200°C.
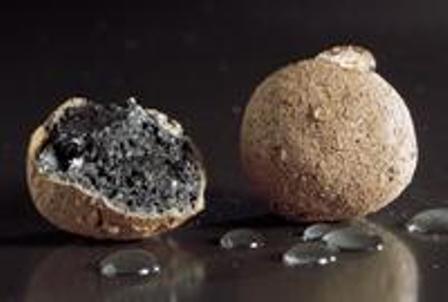
Per l'azione combinata della pressione dei gas che si sviluppano al suo interno durante il riscaldamento e del movimento rotatorio, l'argilla espande, nella fase quasi fluida, nella forma di palline rotondeggianti. Il materiale viene quindi estratto dal forno e sottoposto all'effetto di correnti d'aria che, raffreddando rapidamente l'argilla ed ossidandola, ne provocano la 'clinkerizzazione' superficiale. Il risultato è un nucleo interno poroso che garantisce leggerezza e capacità isolante ed una scorza esterna dura di consistenza vetrosa che fornisce resistenza meccanica.
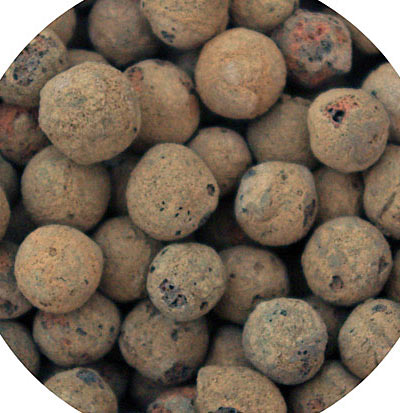
Variando la temperatura, la rotazione ed altri parametri è possibile controllare la densità e la granulometria del prodotto finito. In genere, il peso finale dell'argilla espansa è di circa 1/4 di un comune inerte da cava ( ghiaia, sabbia, etc).
E' un materiale non infiammabile, resistente agli agenti chimici ed atmosferici, con capacità di isolamento termoacustico. Al contrario della vermiculite, ha una notevole resistenza alla compressione. Viene utilizzata per la realizzazione di calcestruzzi leggeri, cortine tagliafuoco, coperture, solai e pareti isolanti, nel drenaggio di terreni ed altri vari impieghi in agricoltura.
Vermiculite
La Vermiculite è un minerale naturale argilloso non molto dissimile dalla mica. Ha una struttura cristallina a tre strati composta da idrosilicati di magnesio ed alluminio che trattiene acqua. Quando viene scaldata a circa 350°C comincia a diminuire di volume, ma oltre i 400°C l'acqua contenuta nella matrice cristallina viene completamente rilasciata, e le lamelle cristalline si espandono, con formazione di micropori che trattengono aria e facendo assumere al minerale l'aspetto da cui deriva il nome. Durante questo processo, la vermiculite aumenta il proprio volume di circa 10-20 volte e diminuisce di conseguenza il proprio peso specifico. La vermiculite esfoliata ha pochissima resistenza meccanica, ma una conduttività termica molto bassa che la rende un eccellente materiale isolante. Viene spesso utilizzata come inerte nei getti di calcestruzzo che debbano avere capacità isolante.
Gli impieghi sono comunque molteplici, sia in edilizia che in agricoltura. E' un materiale inodore, inerte chimicamente, non infiammabile, imputrescibile e resistente all'invecchiamento, insolubile in acqua, sterile, non in grado di formare particelle volatili, resistente ad insetti e microrganismi, in grado di assorbire grandi quantità di liquidi. Trova impiego come materiale isolante sia termico che acustico, nella produzione di cementi leggeri, nei rivestimenti antincendio, come fissativo per liquidi nocivi e assorbente di impurità e di odori, come materiale filtrante, come materiale per imballi, ha molti impieghi in agricoltura ed orticoltura.
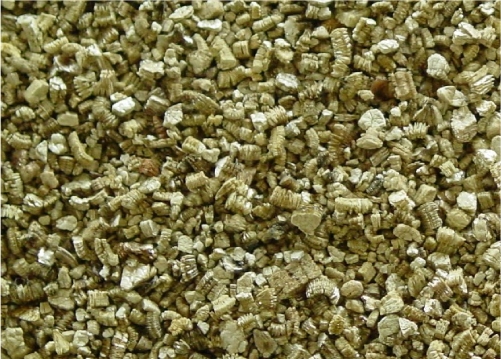
Perlite espansa
Perlite è il nome generico di una varietà di roccia vulcanica silicea, una sorta di vetro naturale, che ha la particolarità, quando sottoposta ad adeguata temperatura, di espandersi sino a 20 volte rispetto al suo volume originario. La roccia originaria si presenta nei più svariati colori, grigio, rossiccio, rosa, giallognolo o verdognolo, mentre, dopo la cottura e l'espansione, il colore è sempre bianco, talvolta tendente al grigio chiaro. La perlite cruda contiene acqua fissata chimicamente in una percentuale che varia dal 2 al 6%.
La perlite è un prodotto inorganico, stabile e chimicamente inerte, sterile ed inattaccabile dai microrganismi, a ph neutro. La perlite espansa si presente sotto forma di piccoli sferoidi di 4/5 mm di diametro.
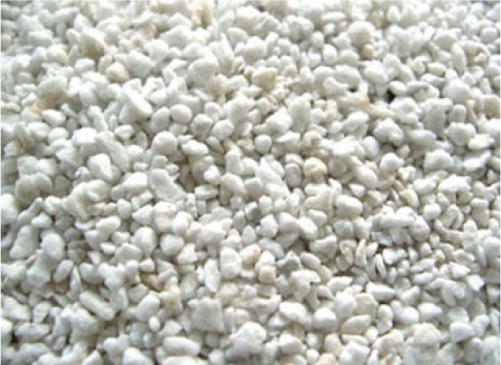
E' utilizzata in edilizia come isolante termico ed acustico, come inerte nei calcestruzzi, cui conferisce proprietà isolanti e di resistenza al fuoco, per l'isolamento di solai, pareti e pavimenti, per l'isolamento di canne fumarie, per la produzione di intonaci isolanti e resistenti al fuoco, ovvero, impastata con argilla, per la realizzazione di mattoni refrattari isolanti. In orticoltura è utilizzata per l'integrazione di substrati colturali cui conferisce capacità di ritenzione idrica e di aerazione.
Nell'industria è utilizzata come abrasivo per saponi speciali, per la realizzazione di filtri per acque pubbliche e piscine, come isolante per celle frigorifere e vasche termostatiche.
Fibre minerali
Il termine fibra si riferisce a qualunque corpo solido di forma allungata e sottile, la cui lunghezza sia tale da superare di molte volte - da qualche decina a diverse migliaia - il suo diametro. Tutte le fibre possiedono, almeno in qualche misura, proprietà tessili, e le fibre minerali non fanno eccezione.
Esistono centinaia di fibre minerali, ma le più comuni sono la fibra di vetro, la fibra ceramica, la lana di roccia.
Fibra di vetro e fibra ceramica
La composizione delle fibre di vetro e delle fibre ceramiche è simile. I componenti fondamentali sono ancora una volta l'ossido di silicio e l'ossido di alluminio in proporzioni variabili. Nelle fibre di vetro sono presenti anche ossidi alcalini, come ossido di calcio ed ossido di manganese, che nelle fibre ceramiche sono invece praticamente assenti
I componenti vengono riscaldati a temperature variabili dai 1800°C ai 2000°C fino a raggiungere lo stato liquido. La massa fluida viene quindi forzata attraverso una trafila microforata da cui emergono delle fibre dello spessore di pochi micron, che vengono quindi raffreddate.
Il prodotto così ottenuto viene sottoposto a varie successive lavorazioni complementari, a seconda dell'utilizzo finale del prodotto, come la feltratura con resine organiche, l'accoppiamento con supporti di varia natura, il confezionamento.
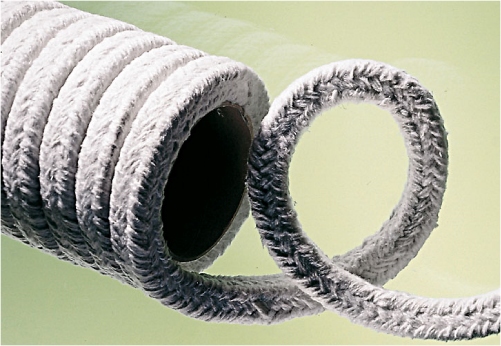
Le fibre di vetro resistono a temperature di circa 500-600 °C, mentre le fibre ceramiche hanno una resistenza termica che raggiunge i 1200 °C
Le caratteristiche generali di queste fibre sono la resistenza termica, la capacità isolante, la resistenza agli shock termici, l'incombustibilità, la buona stabilità dimensionale, l'ottima flessibilità, la buona resistenza agli aggressivi chimici e meccanici.
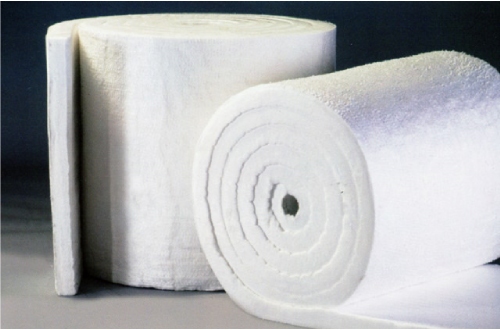
Le fibre possono essere lavorate tessilmente per produrre cordoni, trecce, nastri, tessuti, materassini, etc. L'impiego varia a seconda della densità del prodotto, della sezione e della specifica composizione della fibra, etc.
In edilizia, specie la fibra di vetro, trova utilizzo come materiale isolante e/o coibentante termico ed acustico. La fibra ceramica, tra l'altro, trova impiego nella produzione di stufe per la realizzazione di guarnizioni ad alta resistenza termica.
Lana di roccia e lana di vetro
La lana di roccia è prodotta riscaldando rocce naturali, specialmente basalto o dolomite, sino a circa 1600°C e insufflando poi nella massa semiliquida aria o vapore. Il prodotto finale è una massa di fibre strettamente intrecciate del diametro variabile tra 6 e 10 micrometri. Lo stesso processo può essere applicato ad una massa di sabbia, calcari e ceneri per ottenere la lana di vetro. Alle lane minerali vengono poi aggiunte piccola quantità di resine ed oli per aumentarne la compattezza e diminuire la dispersione di fibre.
Le proprietà della lana minerale derivano dalla sua struttura, una massa di fibre intrecciate che trattiene l'aria, e dalla sua composizione chimica. La lana minerale è chimicamente inerte, non assorbe nè acqua nè umidità, non fornisce supporto alla crescita di microrganismi, quali funghi, muffe e batteri.
La lana minerale viene commercializzata in pannelli e rotoli, il cui impiego principale in edilizia è l'isolamento termico ed acustico degli edifici.
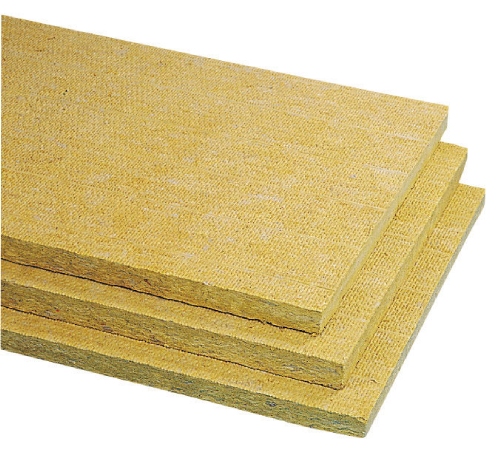
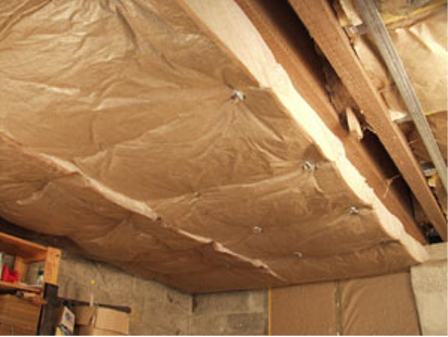
La lana di roccia ad alta densità trova impiego nell'isolamento delle canne fumarie prefabbricate in acciaio, e nella costruzione delle cappe isolate termicamente per l'installazione di termocamini ed inserti da riscaldamento a legna ( foto sotto). Viene generalmente fissata su supporti cha aiutano la lavorazione, cartoni o guaine catramate per impieghi edilizi, una sottile banda di alluminio per la maggior parte delle altre applicazioni
Qualche precauzione va osservata nel maneggiare le lane minerali, che possono disperdere nell'ambiente piccole quantità di microfibre che possono essere irritanti per inalazione o per contatto con la pelle e gli occhi, più che altro per la loro ruvidità.
Contrariamente a quanto alcuni credono, la lana minerale artificiale non è cancerogena. Il 16 ottobre 2001 lo IARC (International Agency for Research on Cancer), nell'ambito del programma di rivalutazione dei rischi carcinogenici dovuti alle MMMF (Man Made Mineral Fibres - Fibre minerali artificiali) ha deciso che queste sono da considerarsi non classificabili come cancerogene per l'uomo. (Rif. Monografia IARC Vol. 81 - 2002)
La legislazione Europea è attualmente un po' più restrittiva: l'ultima direttiva in materia risale al 1997 (Direttiva 97/69/CE) e non recepisce ancora le osservazioni dello IARC, tuttavia, ammettendo che la materia era, all'epoca dell'emissione della norma, ancora oggetto di studio, pur stabilendo parametri generali restrittivi per l'impiego di fibre artificiali vetrose, stabilisce anche le condizioni di esonero da tali restrizioni attraverso il rispetto dei requisiti presenti nella nota Q di tale direttiva. Tutti i prodotti di qualità presenti sul mercato rispettano comunque tali requisiti.
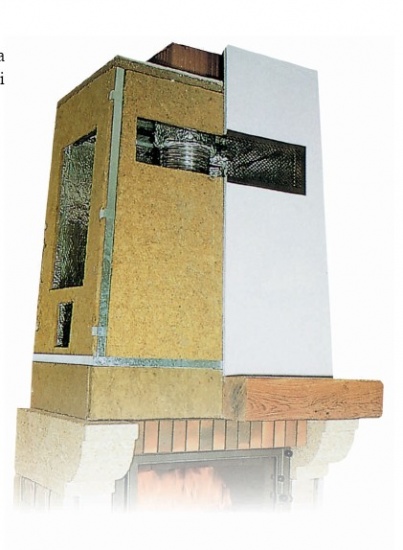
Vetri ceramici
Un accenno meritano le vetroceramiche. Questo materiale relativamente nuovo viene ottenuto da prodotti allo stato vetroso (di per sè non cristallini) mediante trattamento termico di cristallizazione controllata. Si consideri che la composizione chimica del vetro comune è molto simile a quella dei componenti principali delle argille, cioè gli idrosilicati di alluminio, che possiedono una struttura cristallina.
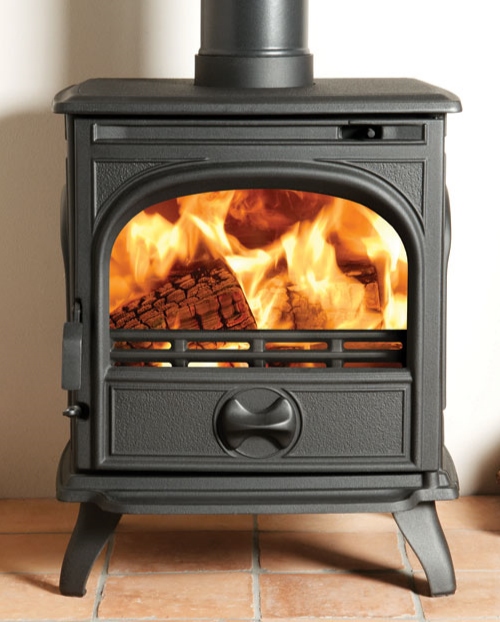
L'ossido di silicio è il componente fondamentale del vetro, così come di molti materiali ceramici e refrattari. Il Vetroceramico è una lega di ossido di silicio, ossido di alluminio e piccole percentuali di ossido di manganese e di titanio. Senza entrare in particolari troppo tecnici, nuovi metodi di produzione conferiscono a questi vetri caratteristiche meccaniche e termiche proprie della ceramica, rendendoli adatti a resistere alle alte temperature ed agli sbalzi termici.
Le vetroceramiche hanno fornito nuovi materiali alle industrie aereonautiche, missilistiche ed elettriche, ed a noi, più modestamente, la possibilità di godere dei vantaggi di una nuova generazione di stufe e caminetti termici che ci scaldano efficacemente ed in assoluta sicurezza, senza toglierci il piacere della vista del fuoco...